Mastering Modern Weaving: The Evolution and Expertise of Industrial Weaving Machines
Industrial weaving machines are integral to modern textile production, transforming fibers into div…….
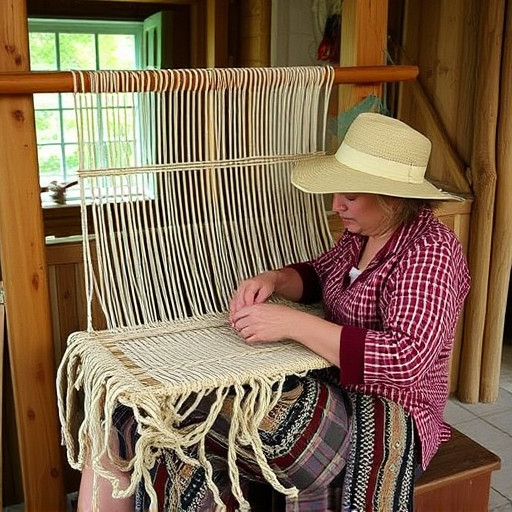
Industrial weaving machines are integral to modern textile production, transforming fibers into diverse woven fabrics with unmatched precision and efficiency. These advanced machines merge mechanical prowess with engineering sophistication to manage the intricate processes of weaving, including yarn distribution and pattern creation. The latest high-speed weaving technologies enable these machines to handle multiple yarns at once, increasing output while maintaining superior quality. The key to their performance lies in the meticulous maintenance of critical components like warping sections and yarn manipulation mechanisms, ensuring consistent production and long-term reliability. The integration of computerized control systems with real-time parameter adjustments, including tension control to prevent defects, enhances the fabrication process. Equipped with sensors, actuators, and automated sizing devices, these systems can produce a vast range of textiles, from simple to complex designs. Their adaptability is further showcased in smart factory settings, where they communicate with other machines and adjust to varying production demands, thus significantly boosting the efficiency and productivity of industrial textile manufacturing.
Industrial weaving machines stand at the core of modern textile production, seamlessly blending tradition with cutting-edge technology. This article delves into their mechanics, tracing the evolution from rudimentary looms to sophisticated automatons that have revolutionized the industry. We’ll explore the integral components and functionalities that define high-performance weaving systems and how they cater to a myriad of fabric needs across various industries. Additionally, we’ll provide insights into best practices for maintenance and operations to ensure peak performance and superior quality outputs. At the heart of it all, understanding these machines not only enhances efficiency but also shapes the future of textile manufacturing.
- Understanding the Mechanics of Industrial Weaving Machines: The Foundation of Textile Production
- Evolution and Advancements in Weaving Technology: From Traditional Looms to Modern Automatons
- Key Components and Functionalities of High-Performance Weaving Systems
- Types of Weaving Machines: Tackling Different Fabric Needs and Industries
- Maximizing Efficiency and Quality with Industrial Weaving Machines: Best Practices for Maintenance and Operations
Understanding the Mechanics of Industrial Weaving Machines: The Foundation of Textile Production
Industrial weaving machines are integral components of modern textile production, orchestrating the intricate process of transforming fibers into woven fabrics. At the heart of their operation lies a complex interplay of mechanics and engineering principles. These machines utilize a series of rollers, shuttles, and mechanisms to manipulate yarns with precision, creating patterns and textures that are essential for various types of materials, from lightweight silks to heavy-duty canvases. The advancement in technology has led to the development of high-speed weaving machines capable of handling multiple yarns simultaneously, increasing efficiency and output.
The mechanics of industrial weaving machines are a testament to human ingenuity in adapting machinery to meet the demands of textile manufacturing. Key components such as the warping section, which distributes yarns evenly onto bobbins, and the healds and reed, which control the lifting and sett of the yarns, work in concert to produce a consistent and high-quality woven fabric. The precision of these components is paramount, as even minor deviations can affect the final product’s quality. Maintenance and regular servicing are crucial to ensure optimal performance and longevity of the machines, directly impacting the production process and the end products’ characteristics. Understanding the mechanics and optimizing their operations form the foundation upon which efficient textile production is built, highlighting the importance of weaving technology in the industry.
Evolution and Advancements in Weaving Technology: From Traditional Looms to Modern Automatons
Key Components and Functionalities of High-Performance Weaving Systems
Industrial high-performance weaving systems are intricate pieces of machinery that consist of several key components and functionalities designed to optimize efficiency and precision in the production process. At the heart of these systems lies the rapier or shuttle mechanism, which is responsible for the actual weaving process by precisely inserting the weft yarns between the warp yarns under high-speed operation. This mechanism ensures tight and consistent stitch formation, which is crucial for the durability and quality of the final fabric. The control system in these machines is sophisticated, often incorporating computerized technology that allows for real-time monitoring and adjustment of the weaving parameters. This includes tension control, which maintains uniform yarn tension throughout the weaving process to prevent any defects or irregularities in the woven fabric.
In addition to the core weaving mechanism, these systems are equipped with advanced sensors and actuators that provide feedback for continuous optimization. The integration of automated sizing devices and dobby or jacquard mechanisms allows for complex pattern weaving, opening up a wide range of textile possibilities from simple flat fabrics to intricate patterns suitable for high-fashion apparel. The machines are also designed with maintenance in mind, featuring easily accessible components and modular systems that enable quick servicing and repairs, thus minimizing downtime. With a focus on automation, these weaving systems can be integrated into larger smart factory environments, where they can communicate with other machinery and adapt to changing production demands, thereby enhancing the overall efficiency and productivity of the industrial textile manufacturing process.
Types of Weaving Machines: Tackling Different Fabric Needs and Industries
The realm of industrial weaving machines is diverse, catering to a myriad of fabric needs across various industries. These machines are pivotal in transforming yarns into woven patterns that serve functional and aesthetic purposes. Among the assortment of weaving machines, the Rigid Heddium Machine (RHM) stands out for producing intricate patterns with a single set of heddles, making it ideal for fine fabrics such as damask and sheers. The Shuttle Less Rapier Machine, on the other hand, is designed for high-speed weaving, suitable for lightweight and delicate materials like silk or nylon where even the smallest imperfections can be detrimental to quality. Another variant, the Air-Jet Loom, excels in producing terry cloths and knitted fabric structures, often found in towels and sweaters. Each type of machine is engineered with specific weaving techniques to accommodate the unique requirements of the textile industry, from high-density fabrics for automotive interiors to fine suits and everything in between. The evolution of these machines reflects a symbiotic relationship between innovation and fabric performance, ensuring that weaving technology remains at the forefront of the textile industry’s ever-changing landscape. Weaving machine manufacturers continuously refine their products to optimize efficiency, durability, and versatility, ensuring that they can meet the diverse needs of modern manufacturing environments.
Maximizing Efficiency and Quality with Industrial Weaving Machines: Best Practices for Maintenance and Operations
Optimal efficiency and superior quality in industrial weaving operations hinge on a robust maintenance and operational strategy. Regular upkeep of weaving machines is paramount, as it ensures that each component operates at peak performance. This includes routine checks and adjustments to tension mechanisms, shedding devices, and yarn guides. Precision in these areas minimizes the occurrence of defects and reduces waste, thereby enhancing the final product’s quality. Additionally, proactive maintenance practices can extend the lifespan of the machinery, mitigate costly repairs, and prevent production downtime.
In parallel with maintenance, operational excellence is achieved through skilled labor and informed decision-making. Operators trained in the nuances of each machine can fine-tune settings to accommodate various yarn types and weaving patterns, ensuring consistent fabric quality. Embracing digital advancements such as automated tension control systems and predictive maintenance software further streamlines operations. These technologies provide real-time data analytics, allowing for quicker responses to potential issues, thus maintaining high efficiency levels and preserving the integrity of the woven materials. By integrating these best practices, weaving businesses can significantly improve their output quality while optimizing resource utilization.