Optimizing Weaving Success: Mastering Warp Tension Control
In the practice of weaving, mastering warp tension is essential for crafting high-quality fabrics ac…….
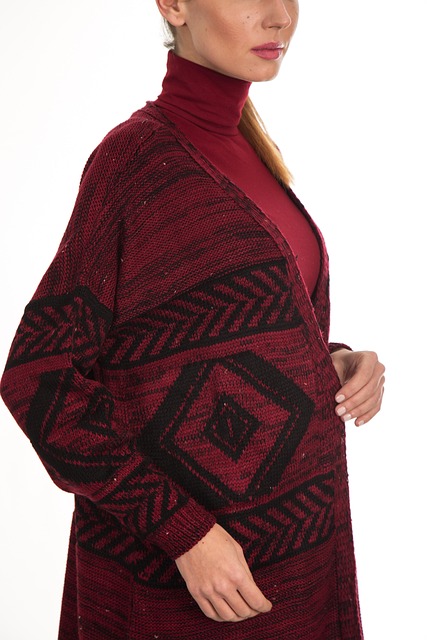
In the practice of weaving, mastering warp tension is essential for crafting high-quality fabrics across various weave structures, from plain to intricate designs like brocades and damasks. Weavers must finely tune their loom settings, considering yarn type, thickness, and material properties to achieve uniformity and prevent issues such as uneven patterns or fabric density. Precise tension management is not only critical for hand weaving but also for industrial looms, which utilize advanced mechanisms like dobby and jacquard systems. The integration of tensiometers and other precision tools allows for real-time adjustments, ensuring the fabric's structural integrity and visual appeal are maintained throughout production. High-tenacity yarns and automated tension control systems further enhance this process by providing stability and consistency. Consistent warp tension control is pivotal for meeting the high standards demanded by contemporary markets, reflecting the sophistication and quality of the woven goods produced. Regular equipment maintenance and systematic approaches to warp setting are key to ensuring the continued success of weaving processes in both traditional and modern contexts.
Weaving is an intricate craft that demands precision, particularly in managing warp tension—the critical aspect determining fabric quality. This article delves into the nuances of maintaining optimal warp tensions for robust and uniform fabrics. It explores the foundational elements affecting warp tention, the mechanics behind its influence on weave integrity, and the techniques for accurate measurement and adjustment. Additionally, it addresses common challenges in managing tension across various weave structures and offers practical tips and best practices for both artisans and industrial weavers to master this essential skill in their craft.
- Understanding Warp Tension in Weaving: The Foundation of Fabric Integrity
- The Mechanics Behind Warp Tension: Factors Influencing Tautness and Slack
- Techniques for Measuring and Adjusting Warp Tension During the Weaving Process
- Common Challenges and Solutions in Managing Warp Tension Across Different Weave Structures
- Mastering Warp Tension: Tips and Best Practices for Artisans and Industrial Weavers Alike
Understanding Warp Tension in Weaving: The Foundation of Fabric Integrity
In the craft of weaving, warp tension plays a pivotal role in determining the quality and integrity of the resulting fabric. The warp threads, running lengthwise from one end to the other of the loom, must be consistently tensioned to ensure that the interlacing weft threads create a stable and uniform fabric. Adequate tension in the warp allows for even shedding and spacing between the warp threads, which is essential for the smooth passage of the weft and prevents issues such as uneven fabric density or patterns that do not align properly. Weavers must carefully calibrate their loom settings to account for factors like yarn type, thickness, and material properties; these adjustments directly influence the tension and consequently the appearance and durability of the woven fabric. Properly adjusted warp tension is not merely a technical aspect but is foundational to achieving a professional-grade weave that can withstand repeated use without distortion or damage. It is through mastering this element that weavers can produce textiles with desirable characteristics, whether for fashion, upholstery, or any other application where precision in texture and strength is paramount.
Mastery of warp tension requires a deep understanding of the interplay between different yarns and their responses to mechanical forces on the loom. Weavers must be vigilant throughout the weaving process, as subtle changes in tension can lead to significant variations in the fabric’s final product. This is particularly critical when working with specialized or delicate fibers that may stretch or break under improper tension. Regular monitoring and fine-tuning of warp tension are necessary to maintain consistent quality across large batches of fabric. Additionally, advanced weaving technologies, such as computer-controlled dobby and jacquard mechanisms, can assist in maintaining precise tension, allowing for complex patterns and designs that were previously difficult to achieve by hand. Understanding and controlling warp tension is thus an indispensable skill for artisans and industrial weavers alike, ensuring the longevity and aesthetics of woven goods.
The Mechanics Behind Warp Tension: Factors Influencing Tautness and Slack
Maintaining the correct warp tension in weaving is a critical aspect of producing high-quality textiles. The warp, consisting of the vertical threads, must be held taut to facilitate the interlacing with the weft, or horizontal threads. The tension of these yarns directly influences the structure and appearance of the final woven fabric. Factors that affect this tension include the type of loom used, the properties of the yarn material, and the specific weaving technique employed. For instance, a mechanical loom relies on precise tensioning mechanisms to maintain consistent warp tension throughout the weaving process. The materials themselves, whether cotton, wool, or synthetic fibers, exhibit different elasticity and weight, which can affect the tautness required for optimal weaving. Additionally, environmental conditions such as temperature and humidity can cause yarns to shrink or expand slightly, potentially leading to slack or overtightness in the warp if not carefully managed. Weavers must therefore calibrate their tension settings according to these variables to ensure a uniform and balanced fabric, which is essential for both aesthetic quality and functional integrity. Attention to detail in this regard can make a significant difference in the durability and finish of the woven product.
Techniques for Measuring and Adjusting Warp Tension During the Weaving Process
Managing warp tension is a critical aspect of the weaving process, ensuring the integrity and quality of the final fabric. Weavers employ various techniques to measure and adjust warp tension effectively. A key method involves using a tensiometer, which directly measures the tension applied to individual yarns in the warp. By positioning the tensiometer between two adjacent warp yarns, weavers can determine the force exerted on each yarn, allowing for precise adjustments. This tool is instrumental in identifying discrepancies that could lead to pattern distortions or fabric defects.
Adjusting warp tension requires both skill and precision. Weavers often make these adjustments during the selvage formation and throughout the weaving process. The use of a well-calibrated back roller can help in reducing the overall tension, while a front roller can increase it. The combination of these mechanisms, along with the tensiometer’s readings, enables weavers to fine-tune the tension to the desired specifications. Regular monitoring and incremental adjustments are essential to maintain consistent tension across the entire warp, which in turn guarantees a uniform and high-quality fabric. Weaving machines equipped with automated tension control systems further facilitate this process, providing digital readouts and automatic corrections to compensate for any variations in tension during production. These advancements in weaving technology enhance the precision of the craft and contribute to the efficiency of the manufacturing process.
Common Challenges and Solutions in Managing Warp Tension Across Different Weave Structures
In weaving, maintaining consistent warp tension is paramount to achieving a quality fabric. Weave structures vary from simple plain weaves to complex jacquards and satins, each presenting unique challenges in tension management. One common challenge is the uneven distribution of tension across the warp threads, which can lead to patterns misaligning or the fabric having an undesirable texture. This issue is particularly prevalent in structures like twills and satins, where the design relies on precise thread placement. Solutions to this problem often involve careful selection of yarn types and weaving technologies. High-tenacity yarns can maintain their tension better, reducing the need for frequent adjustments during the weaving process. Additionally, the use of modern looms equipped with tension control systems allows for real-time monitoring and adjustment of individual warp threads, ensuring uniformity across the entire fabric width. These advanced systems can be particularly beneficial when transitioning between different weave structures within the same piece of cloth, as they help maintain consistent tension regardless of the complexity of the pattern.
Another challenge in managing warp tension is the variation that occurs with changes in yarn density and pattern complexity. In intricate patterns such as those found in brocades or damasks, maintaining consistent tension becomes even more critical to preserve the integrity of the design. To address this, weavers may implement a variety of strategies, including pre-treating yarns to stabilize their behavior under tension and employing computer-controlled dobby or Jacquard mechanisms that can handle complex pattern drafts with precision. These systems work in tandem with the loom’s tension control system to produce fabrics with intricate patterns and even texture, ensuring that the final product meets the high standards required for such detailed weave structures. By mastering these techniques, manufacturers can produce fabrics with consistent warp tension across diverse weave structures, leading to a superior end product.
Mastering Warp Tension: Tips and Best Practices for Artisans and Industrial Weavers Alike
Mastering warp tension is a critical aspect of successful weaving, whether one is an artisan working on a small handloom or an industrial weaver operating large-scale machinery. The tension of the warp threads has a profound impact on the integrity and appearance of the final woven fabric. For artisans, inconsistent warp tension can result in patterns that do not align correctly, leading to visual imperfections. Conversely, for industrial weavers, poor tension management can lead to increased wastage, reduced production efficiency, and even mechanical issues with the loom itself.
To achieve optimal warp tension, it is essential to understand the materials being used and the desired outcome of the weaving process. Begin by selecting high-quality yarns suitable for your project, as variations in yarn quality can significantly affect tension. Carefully measure and secure the warp threads before beginning to weave; this sets a stable foundation. Regularly check the tension of the warp throughout the weaving process using a tensiometer or a hand-feeling method. Adjustments should be made as needed, which may involve changing reed dents, tying off sections, or slightly altering the take-up mechanism on the loom. Additionally, artisans and industrial weavers alike benefit from consistent practice; the more experienced one becomes, the more intuitively one can detect and correct warp tension issues. Employing a systematic approach to warp setting and regular maintenance of equipment ensures that the tension remains constant, leading to uniform and high-quality woven products.