Weaving Evolution: From Manual to Automated Efficiency and Future Sustainability
Industrial weaving machines have evolved dramatically over centuries, from hand-powered looms to sop…….
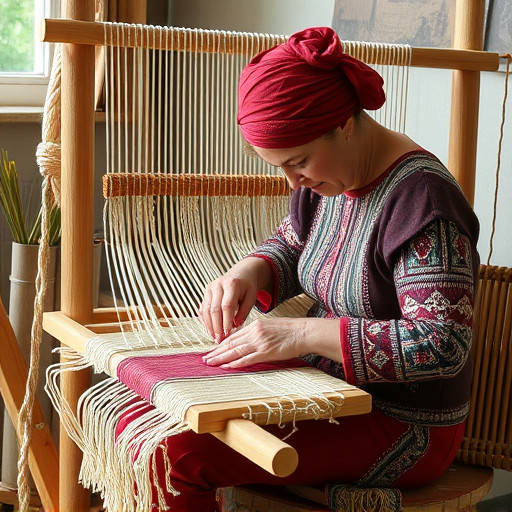
Industrial weaving machines have evolved dramatically over centuries, from hand-powered looms to sophisticated computer-controlled systems. Early innovations like Edmund Cartwright's power loom automated weaving, boosting production speed and efficiency. Subsequent developments, including electric and CAD systems, enabled complex patterns and precise control. Today, AI and robotics drive weaving technology, offering intricate designs, sustainable materials, and revolutionized fabric production. These advanced machines automate key stages, increase productivity, and enable the rapid manufacture of diverse fabrics, enhancing cost-effectiveness in today's market. While facing environmental concerns, the industry is adopting eco-friendly practices with efficient water recycling systems, renewable energy sources, and advanced material handling technologies to reduce its carbon footprint.
“Discover the remarkable journey of industrial weaving machines, from their historic roots to modern innovations. This article explores the evolution of weaving technology, charting the progression from manual labour to cutting-edge automation. Uncover the diverse types of machines that drive fabric production efficiency and learn how these advancements impact the textile industry. We delve into environmental considerations, highlighting sustainable practices within industrial weaving, as the sector navigates a greener future.”
- History and Evolution of Industrial Weaving Machines
- Types of Weaving Machines: From Manual to Automated
- How Industrial Weavers Enhance Fabric Production Efficiency
- Modern Innovations Shaping the Future of Weaving Technology
- The Environmental Impact and Sustainability in Industrial Weaving Machines
History and Evolution of Industrial Weaving Machines
Industrial weaving machines have a rich history dating back centuries, evolving from simple hand-powered looms to sophisticated computer-controlled systems. The early days saw the introduction of mechanized looms in the 18th century, marking a significant shift in the textile industry. These early machines, like Edmund Cartwright’s power loom, revolutionized weaving by automating the process, increasing production speed and efficiency.
Over time, technological advancements drove further evolution. The 19th century brought innovations such as the flying shuttle and water-powered looms, enhancing productivity. The 20th century witnessed the rise of electric and computer-aided design (CAD) systems, enabling more complex patterns and precise control. Today, industrial weaving machines incorporate advanced technologies like artificial intelligence and robotics, pushing the boundaries of what’s possible in fabric production, from intricate designs to sustainable materials.
Types of Weaving Machines: From Manual to Automated
The evolution of weaving machines has transformed the textile industry, marking a significant shift from manual labor to automated precision. Traditional handlooms, operated by skilled artisans, have made way for a diverse range of mechanical and digital weaving technologies. These machines vary in complexity and application, catering to different fabric types and production scales.
At the heart of this transformation lie two primary categories: manual and automated weaving machines. Manual looms, though still used in certain traditional crafts, require human dexterity and expertise. Automated systems, on the other hand, leverage advanced mechanisms and computer controls. From simple mechanized looms to sophisticated industrial automatons, these machines can weave intricate patterns at lightning speeds, revolutionizing fabric production and opening doors for innovative textile designs.
How Industrial Weavers Enhance Fabric Production Efficiency
Industrial weavers play a pivotal role in enhancing fabric production efficiency through their advanced machinery and specialized techniques. These machines, designed for large-scale weaving, streamline the process by automating various stages, from thread preparation to yarn weaving and fabric finishing. The result is a significant increase in productivity compared to traditional handwoven methods, allowing manufacturers to meet market demands faster.
Moreover, industrial weavers’ expertise lies in their ability to customize settings and adapt machines for different fabrics and patterns. This versatility enables them to produce a wide array of textiles, from sturdy denim to delicate silk, at an unprecedented pace. By optimizing production lines, these weavers contribute to cost-effectiveness, making fabric manufacturing more accessible and efficient in today’s competitive market.
Modern Innovations Shaping the Future of Weaving Technology
Modern innovations are revolutionizing the world of weaving, pushing the boundaries of what was once thought possible with traditional weaving machines. The introduction of advanced technologies such as artificial intelligence (AI) and machine learning is transforming the way fabrics are created, allowing for greater precision, efficiency, and customization in the weaving process. AI-powered systems can analyze vast amounts of data to predict fabric behavior, optimize thread tension, and even design unique patterns, elevating the art of weaving to new heights.
Furthermore, the integration of robotics and automation has streamlined production lines, reducing human error and increasing output speeds. These innovations are not only enhancing the quality of fabrics but also opening up new possibilities for sustainable practices. For instance, smart fabrics that can adapt to their environment or recycled materials that minimize waste are gaining traction, ensuring a more eco-conscious future for the weaving industry.
The Environmental Impact and Sustainability in Industrial Weaving Machines
The environmental impact of industrial weaving machines is a growing area of concern in the textile industry. These powerful tools, responsible for producing vast quantities of fabric, often come with significant ecological footprints. The production and use of raw materials, energy-intensive processes, and water consumption during weaving can lead to substantial environmental degradation if not managed sustainably. For instance, the extensive use of water in certain weaving techniques may result in water scarcity, especially in regions with limited water resources.
To address these issues, many manufacturers are now focusing on developing eco-friendly weaving machines. Innovations such as efficient water recycling systems, renewable energy sources for power, and advanced material handling technologies aim to reduce the carbon footprint of industrial weaving. These sustainable practices not only benefit the environment but also contribute to a more responsible and long-term future for the textile manufacturing industry, ensuring that the art of weaving can thrive without compromising our planet’s health.